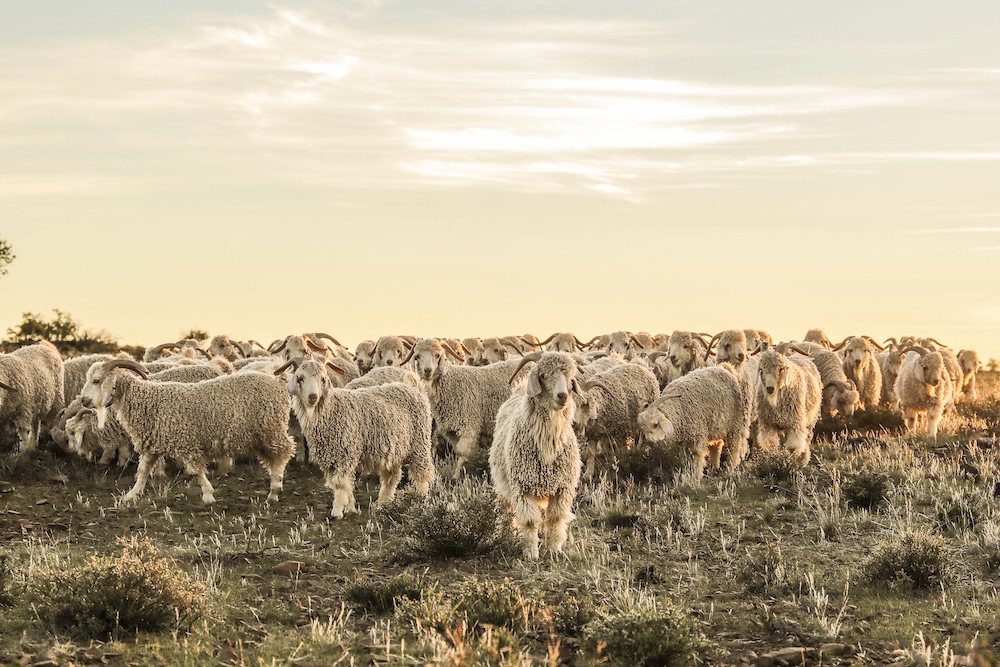
When Lorenza Wong took on responsibility for the Textile Development and Marketing capstone course, she rewrote it from scratch.
Before this year, students had learned about luxury Italian fabrics, working with mills to spin silk and cotton fibers. “As much as I love Italian fabrics, I just feel like it had been done,” says Wong, adjunct assistant professor. Students told her they wanted to learn about sustainable textiles—and she realized they needed to start to understand farming. She wrote a brand new course that focused on craftsmanship, working with artisans, and forging a sustainable livelihood.
Wong herself owns a farm in the Philippines that produces abacá, the raw material for a sturdy high-end plant fiber. In 2023, she traveled to South Africa’s Karoo, a semi-arid region that produces 60% of the world’s mohair, a luxury fiber harvested from Angora goats. She felt a deep connection to the process and product, and she wanted to bring that knowledge to her students.
To contrast the production of animal and plant fibers, she included abacá as the second focus of the course. A third fiber in the capstone curriculum, piña, is extracted from the Red Spanish pineapple, also grown in the Philippines. She included a fourth, Jacob wool, grown in New York State, to give students a glimpse into local production.
Frances Van Hasselt, whose family owns the Angora goat farm that Wong visited, and whose sustainable brand, Frances VH, produces luxury mohair rugs, apparel, and other textiles, came to New York for two weeks in February to help teach the mohair section of the course.
“At a time of heightened technology, there’s been this pullback to handmade artisanal pieces that are connected to people and the earth,” Van Hasselt says. “There’s a comfort and soul that these pieces have—it’s something that mechanized and mass-produced objects can never give us.”
In the course, TD 476, eighth-semester students learn about the farms that produce these four fibers, and they explore the fibers in a hands-on, intensive way. They learn about spinning, dyeing and finishing, and weaving and knitting, and they conclude by making a sample textile of their own. Journal reflections throughout the semester allow them to discover their personal and professional mission.
“Until you feel the fibers and see behind the scenes, you don’t really get connected to them,” Wong says. “I want them to understand they can do this. It may not work for every model, but it can work, and they can take it to the next level.”
“We’re doing this course because we feel like there’s so much broken in the fashion and textile world, yet we keep educating in exactly the same way,” Van Hasselt adds. “We need to fix that.”